

Laserax has developed laser cleaning machines that require very little effort on the part of users.
Laser blaster for rust manual#
It is possible to affect very localized area without tapingĪ range of handheld, manual and automated solutionsĬontact a Laser Expert Laserax Laser Cleaning Machines Modularized Laser Cleaning Solutions for Industrial Applications Most applications require no PPE and no training Relatively high initial capital expenditure is required Video 1 - Laser cleaning compilation Disadvantages of Laser Cleaning Click the image below to start the video demonstrating Laserax’s laser cleaning systems.
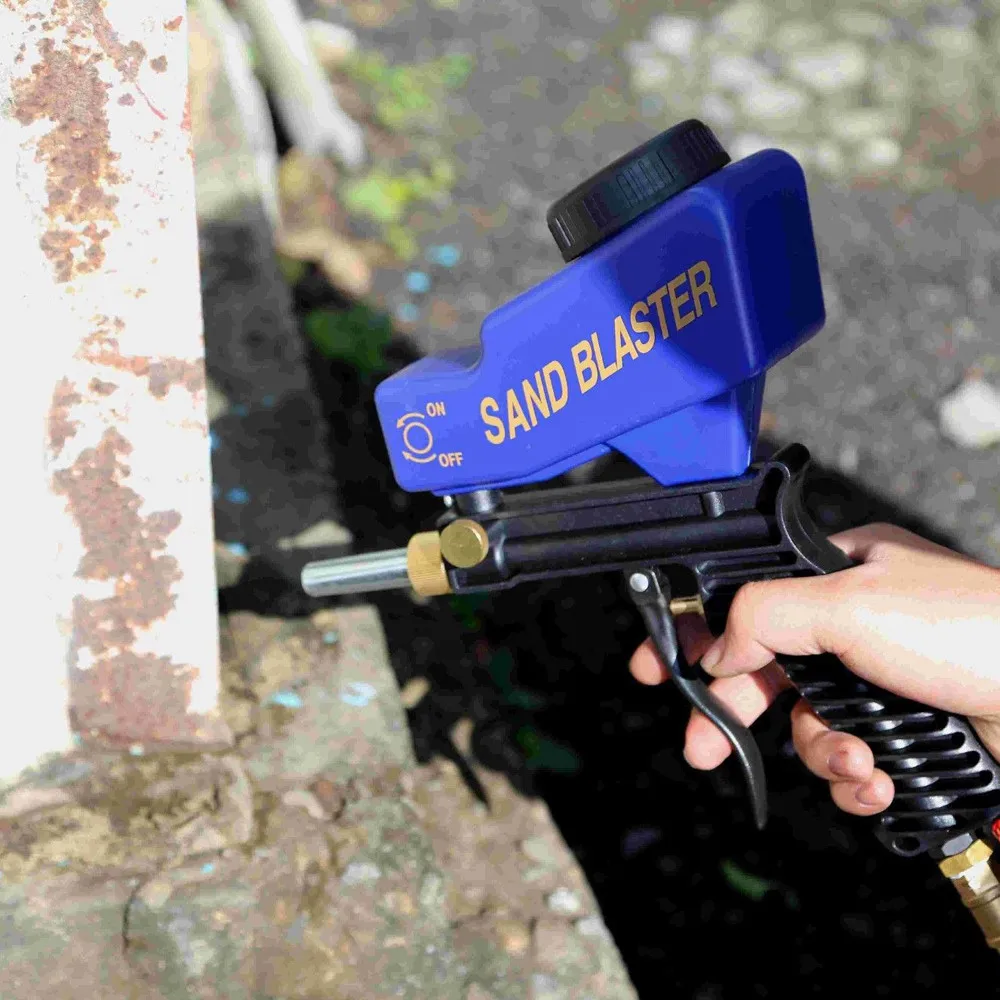
The video also illustrates the ability of our laser systems to manage complex surfaces (round, inclined and V-shaped). You will see, in the following video, Laserax’s lasers removing rust on steel and cleaning heat stain on stainless steel weld. Since workers are not exposed to harmful laser beams, there is no need for personal protective equipment (PPE), special training and other user control measures. They serve the same purpose as the shotblast cabinets shown in the images above. These enclosures prevent exposure to harmful laser beams. Laser Safety ManagementĪs far as safety goes, Laserax specializes in automated industrial laser solutions that use Class 1 laser safety enclosures. This is true even when you pass several times on a material at intensities below its ablation threshold. Otherwise, nothing happens to the material, except for a slight localized temperature increase. If the intensity of the laser is above the ablation threshold of the material, it will have an impact on the material. The minimum intensity required to affect a material is called the ablation threshold.įigure 2 - Illustration of laser cleaning It so happens that contaminants usually require less energy per unit surface to be vaporized than the surfaces they reside on. The power that is transmitted increases the temperature of the contaminants to the point that they are vaporized. Laser ablation vaporizes the contaminants through the emission of short pulses of high levels of energy to very small surfaces. However, it uses laser ablation to remove the contaminants with little to no impact on the underlying material. Laser cleaning may serve a similar purpose than sandblasting: removing rust, different oxides, oil, grease and paint.
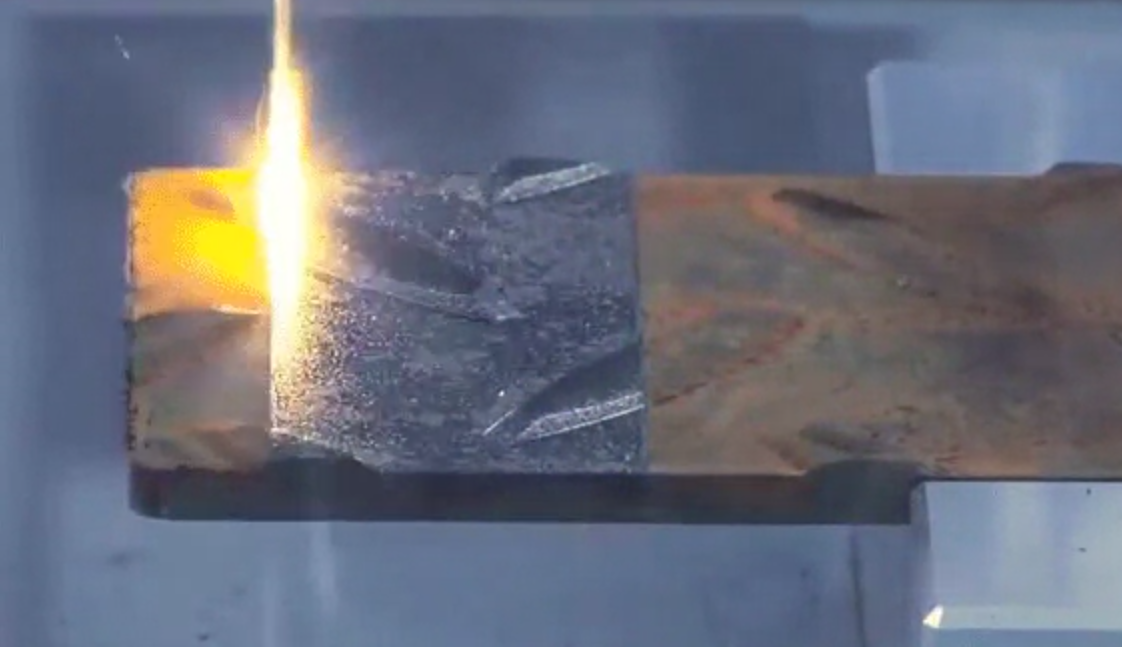
Laser Cleaning as an Alternative to Sandblasting It is a known technology that dates back to the 1910sĮnvironment, health and safety risks are easy to manage Personal Protective Equipment (PPE) for large sandblasting installation is cumbersome Rust, different oxides, oil, grease, and paint are commonly removed by sandblasting.įigure 1 - Inside a typical shotblasting cabinet (2) Disadvantages of sandblastingĬosts may become prohibitive for large installationsīlasting media need to be recycled and replaced from time to time The abrasive material is propelled by compressed air or by water.(1) It can serve different purposes however, its most popular use is the removal of surface contaminants. Sandblasting, or abrasive blasting, is the material processing that results from the propulsion of an abrasive material under high pressure to a surface. This innovative technique effectively cleans surfaces, prepares them for coating or welding, removes rust, and strips paint, all while minimizing damage to the material, ensuring an environmentally-friendly and cost-effective solution for diverse industries.Ĭontact a Laser Expert What is Sandblasting? Laser cleaning is a safer, non-abrasive alternative to sandblasting for various applications.
